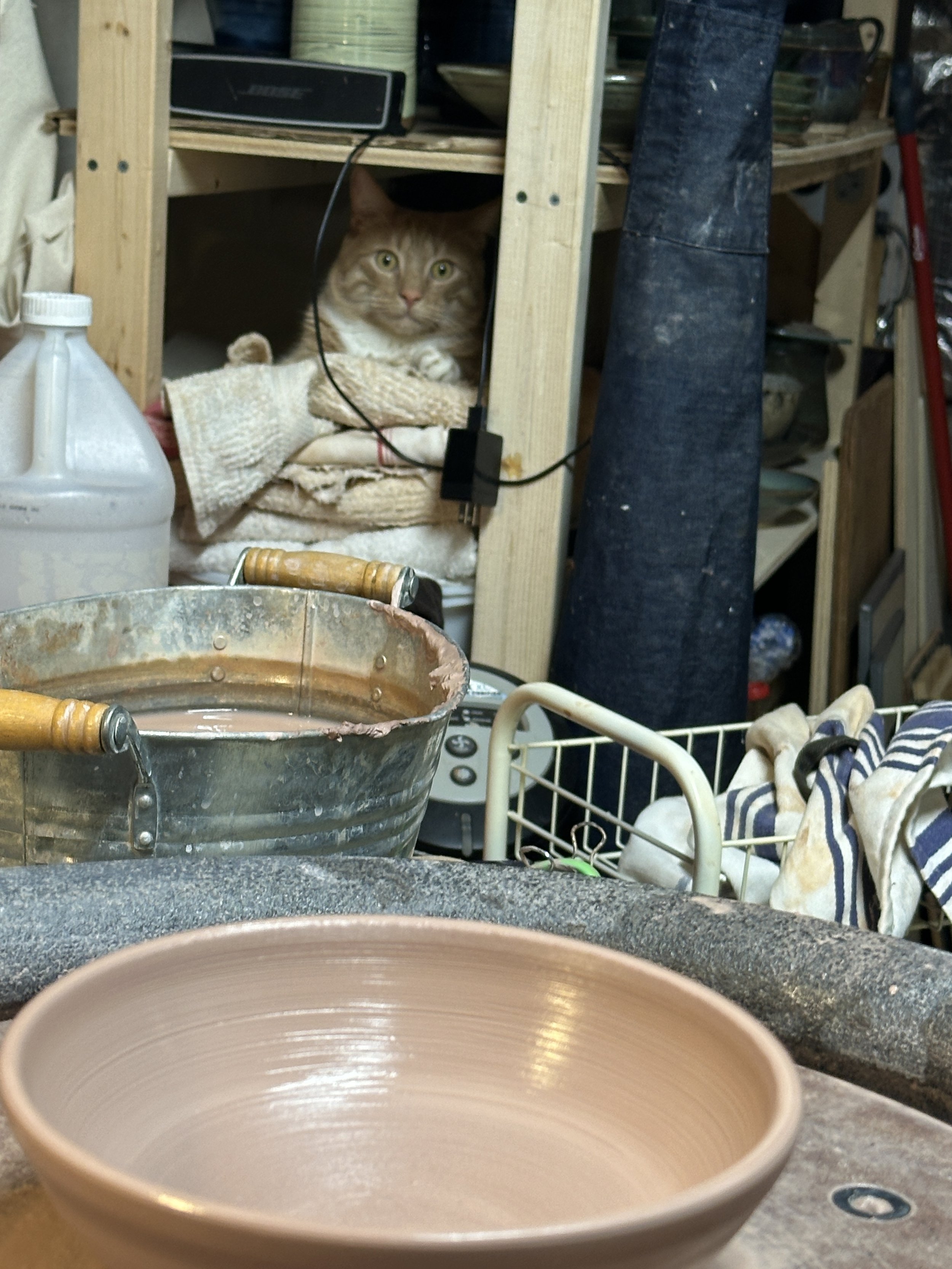
The process of pottery making
I first start with wet clay. All my work is currently using Stoneware clay. I use a variety of clay bodies from smooth white, grays, light and dark browns to red and black clay. The textures are smooth to sandy clay, clay with added Iron and manganese to add tooth and effects to the glaze
Here’s Neo hanging out with a fresh bag of clay ready to be worked
I first wedge the raw clay to wake it up a bit and to make sure all of the air bubbles are worked out of it
The clay is then centered on the wheel and worked until the desired form is created
Trimming - I like to trim as little as possible. This process allows me to define shape and style in my hands at the beginning stages rather than relying on the use of a trimming tool. I feel it is a bit more of an organic process and more demanding to work with the structure of the design.
First Firing - Bisque. I slow fire my greenware and use a hold at 185 degrees of 2 to 6 hours just to make sure my ware is fully dry. This keeps it from going to the boiling point which would explode the pots. The top temperature reached is around 1945 degrees F.